Building the Lean Organisation
Introduction- A Journey into Time
Toyota conceptualised, designed, developed and delivered a production methodology post-World War II that would fundamentally alter the industry in years to come. The inefficiencies of the conventional production model were addressed by the development of the Toyota Production System (TPS). It concentrated on maximizing output by getting rid of systemic waste. Companies may then offer the highest-quality goods and services at the most affordable prices and with the shortest lead times.
In our previous episode, we promised to do deeper dive into the Lean paradigm where the components of the House of Lean or the Toyota Production System (TPS) would be explained to give practical pointers on how your organization could start its own Lean journey. Here we go!
The House of Lean
The House of Lean (Fig. 1) depicts how Lean would be implemented in an organization. It depicts the Lean methodology as a house, with the building blocks seamlessly integrated to deliver the ultimate construct- CUSTOMER SATISFACTION. The House of Lean allegory represents the fundamental principles, ideas, tools, techniques, and tenets that have underpinned Toyota’s success, as well as how TPS has evolved into the world’s gold standard for manufacturing excellence. Using the Lean methodology, this graphic representation assists businesses in designing and optimizing their operations. It focuses on the three basic requirements of an operational strategy: people, process, and technology.
It is common knowledge that every building begins with the foundation, so we would begin by deconstructing the Lean paradigm there. Before beginning any type of lean implementation, a company must lay a solid foundation because this foundation will support the rest of the infrastructure. We will go on from there to understand the pillars, the roof and the interior constructs.
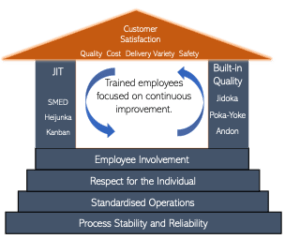
- The Foundational Building Blocks
Process Stability and Reliability. Not your usual English words– but the scientific and statistical meanings thereof. Stability in process lingo refers to processes that have all special causes of variation removed and that are working within their natural limits in a controlled manner with as little variation as possible. Reliability refers to the likelihood that a product, system, or service will perform its intended function adequately for a specified period or will operate without failure in a defined environment. Isn’t it obvious that these characteristics should be at the heart of any Lean initiative? The onus falls on organizational leaders seeking to implement Lean initiatives to understand the causes of variation and potential failures in their critical processes and to design programmes to reduce and properly manage these core parameters.
Standardised Operations. It is worthy to cite a Henry Ford quote here:
“To standardize a method is to choose out of the many methods the best one and use it. Standardization means nothing unless it means standardizing upward. Today’s standardization, instead of being a barricade against improvement, is the necessary foundation on which tomorrow’s improvement will be based. If you think of “standardization” as the best that you know today, but which is to be improved tomorrow – you get somewhere. But if you think of standards as confining, then progress stops.”
Standardization increases productivity by removing inefficiencies. This is the result of removing ambiguity and providing quality control: tasks are completed more efficiently, and there are fewer quality control issues as a result of tasks that were not completed correctly the first time. Standards paint a clear picture of the desired state. We can’t tell normal from abnormal without them. Good standards are simple, clear, visual, and adhered to, and they serve as the foundation for all improvement activities.
Respect for the Individual. The Japanese word for respect is sonkei suru (人間性尊重). The English transliteration is: “We treat others as they want to be treated…with courtesy, dignity and consideration”. Toyota does not use one simple, discrete definition to express the “Respect for People” principle, whose context is better represented by the phrase “Respect for Stakeholders”. Rather, it is a more elaborate multi-layered description that includes historical words from former Toyota executives to better comprehend its meaning. Toyota’s top-level representation of the “Respect for People” principle consists of two parts: “Respect” and “Teamwork,” and is as follows:
- “Respect: We respect others, make every effort to understand each other, take responsibility and do our best to build mutual trust.
- Teamwork: We stimulate personal and professional growth, share the opportunities of development and maximize individual and team performance.”
Employee Involvement. At the heart of the Toyota operating system is a winning and inclusive culture where flexible, motivated employees continuously solve problems. It encompasses strategies geared towards developing learning, strength, and capability within the organization. The key tenets underpinning this foundational block are:
- The success of our company depends on our people!
- We must unleash the full potential of our people through:
- Winning and inclusive culture
- Teamwork
- Continuous improvement.
- The Pillars
Built-in Quality. Edwards Deming says it best in the third of his Fourteen Principles: “Cease dependence upon inspection alone. Build quality into the process from start to finish. Inspections are costly and unreliable – and they don’t improve quality, they merely find a lack of quality.” Built-In Quality is a Lean management practice that aims to proactively address quality issues before they become large-scale problems through the use of continuous improvement tools in the manufacturing process. The same principle would apply to the operations of the service industry. A number of Lean implements would help organisations to implement this ideal.
- Jidoka is a Lean method that is commonly used in manufacturing and product development. It is a simple way to protect your company from delivering low-quality or defective products to your customers. It is also known as autonomation. It refers to the implementation of devices and systems that stops a machine or a process whenever a defective product is detected or produced. Jidoka systems help to discover abnormalities, stop the process, fix the immediate problem, and further investigate and solve the root cause
- Poka-yoke means mistake-proofing; and refers to devices and systems that can be designed to prevent defects from occurring.
- Andon is a visual control device in a production area, typically a lighted overhead display, giving the current status of the production system and alerting team members to emerging problems.
Just-in-Time Production involves having the parts and machinery ready as soon as possible before it is required. As a result, there will be less downtime and money spent on warehousing products before they are needed. In essence, producing or conveying only the items that are needed by the next process when they are needed and, in the quantity, needed. Lean systems support this through the implementation of systems and techniques such as:
- SMED SMED (Single-Minute Exchange of Die) is a system that drastically reduces the time required to complete equipment changeovers. The SMED system’s essence is to convert as many changeover steps as possible to “external” (performed while the equipment is running), while simplifying and streamlining the remaining steps. The term “Single-Minute Exchange of Die” refers to the goal of shortening changeover times to “single” digits (i.e., less than 10 minutes).
- Heijunka is a Japanese word that transliterates to levelled production. It provides stable demand (information) to the production system, helps to dampen the variation of customer demand and enables standard work and therefore level production (every product every interval). By employing this technique, businesses can satisfy client requests while reducing costs and avoiding overproduction
- Kanban – A signalling device that gives instruction for the production or conveyance of items in a pull system. Can also be used to perform kaizen by reducing the number of kanban in circulation, which highlights line problems. Controlling the flow of various materials, goods, information, and other items is critical for any operation. The kanban concept employs signals to show when a specific step in the production process should take place in order to keep everyone informed and improve productivity.
- The Roof
The customer is the first consideration when creating a new concept, service, or product. The roof depicts the organization’s goal: to create the finest quality products at the lowest possible cost and in the quickest lead time. The roof represents Toyota’s goal, which is ‘Best Quality, Lowest Cost, Shortest Lead Time, Best Safety and High Morale”. They’ve stated that they’ll accomplish this “by shortening the production flow and eliminating waste.”
- The Interior
Kaizen (改善) is a combination of two Japanese words that mean ‘good change’ or ‘improvement’. However, because of its association with Lean methodology and principles, the term has come to mean “continuous improvement. The Kaizen ideology refers to trained and empowered employees continuously improving business processes in incremental steps.
In Conclusion: L-E-T’s Go LEAN!!!
Let these guiding principles be central to an organization-wide Lean implementation:
Leadership. Without the support of the leadership teams, Lean initiatives have no chance of becoming successful. This must begin at the top of the organization and descend all the way to the supervisors and the front lines.
Employees – Lean encourages employee participation by welcoming their feedback and considering their ideas.
Trust – Coworkers, management, and departments must all have trust in one another. Building the trust required for a strong foundation can be facilitated by ensuring that everyone is aware that they are all working toward the same goals.
These tenets are captured succinctly in the International Academy for Quality (IAQ) manifesto in these regards:
Create trust and happiness. …create an environment wherein all employees gain security through their experience of prosperity, happiness, trust, and inner confidence through their rising abilities and self-respect.