- Introductory Lean Six Sigma
Background to the Series
I came across the Lean Six Sigma methodology some seventeen odd years ago while working for a Honda first-tier supplier of body-in-white components in the West Midlands of the United Kingdom. The results I saw delivered by the methodology were so mind-blowing that it set me on an almost obsession-driven course to explore and deep-dive into it. And I did!!! This obsession has led to a life-long quest for knowledge, learning, and sharing with others. I’ve had the opportunity to share this knowledge and practice with thousands of professionals, and I’ve assisted organisations of all sizes in using the methodology to improve business processes, reduce operational costs, build staff capacity, increase efficiencies, and drive organisational growth. Over the next six episodes, I will share theory and real-life experiences from this journey, as well as additional lessons on how I have applied and taught this methodology to a wide range of industries (manufacturing, banking, telecommunications, mining, petroleum, public sector organisations, parastatals, and other allied industries) and academia alike. Join me as I deconstruct Lean Six Sigma, and possibly point to the adoption of a model of operational excellence that has revolutionised industry for more than five decades.
Introduction to Lean Six Sigma
Lean Six Sigma (LSS) is a business improvement methodology which combines tools from the two conceptual and practical schools- Lean Manufacturing (based on the Toyota Production System, TPS) and the Six Sigma methodology (originating from Motorola). Lean manufacturing focuses on speed and traditional Six Sigma focuses on quality. By combining the two, the result is better quality faster. The creators of this integrated system sought an approach that concurrently addresses the iron triangle of cost, quality and delivery (speed and reliability). The advantage of combining the two approaches is that where Lean focuses on the removal of waste and reducing lead times, Six Sigma focuses on developing capable processes through the Define, Measure, Analyse, Improve, Control (DMAIC) cycle. Another domain of Six Sigma which applies to designing new products and processes under a general protocol called Design for Six Sigma (DFSS) will be discussed in detail in a later episode.
The roots of the Lean Six Sigma movement may have begun in industrial manufacturing, but its reach has expanded well beyond into all industries including services and transactional processes. In a PricewaterhouseCoopers report titled: ‘Cost Out! A Lean Six Sigma Approach to Drive Out Costs’ (March 2006), a number of world-class companies were listed that had implemented Lean Six Sigma with very high success rates. Notable among them is Boeing, which has used Lean Six Sigma to achieve a 61 percent reduction in assembly time, a 55 percent reduction in work-in-process (WIP) inventory, and a 59 percent reduction in stored inventory. In general, a typical Lean Six Sigma implementation is reputed to be able to reduce inventory by 50 percent in one year, reduce production cycle time by 25 percent in 3 months, and deliver 10 percent to the bottom line compounded annually.
The fusion of Lean and Six Sigma improvement methods (Fig 1) is required because:
- Lean cannot bring a process under statistical control.
- Six Sigma alone cannot dramatically improve process speed or reduce invested capital.
- Both enable the reduction of the cost of complexity.
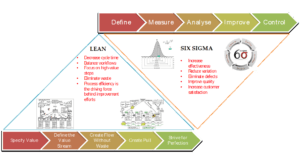
What is Lean?
Lean manufacturing is not an entirely new concept. According to Dirgo (2006:71), it dates back to 1913 when continuous flow was practised at Ford. It is now a collection of practices that the Toyota Motor Company uses in its everyday operations. The Toyota Production System (TPS) may be the most popular manufacturing management system. It is a widely used reference for Lean manufacturing and continuous improvement and has been the base for several companies that have developed and implemented a production system of their own. It has evolved over years of trial and error – with the aim of reducing waste in manufacturing facilities, streamlining processes and operations, and optimising manpower and equipment. Taghizadegan (2006:1ff) describes Lean as a “continuous effort to accelerate and minimise the cost of any process by eliminating the waste”.
Page (2004:236-7) calls Lean the “vision of perfect waste-free manufacturing”. He maintains that in a globally competitive marketplace, the “survivors who are still around in twenty years will be the manufacturers who became lean.” That is where Lean comes in as a tried and tested approach to streamlining industry systems toward world-class manufacturing that commands respect in the marketplace and has a fair share of market earnings. Drew et al (2004), in defining the benefits of Lean Manufacturing, made some very stalwart statements of fact; one very significant one being that: “Lean can transform operations in any sector, opening up new strategic opportunities”.
Womack and Jones (1996) expatiated on the principles of Lean thinking-value, the value stream, flow and pull. They further accentuated the fact that when these principles are properly implemented in a manufacturing environment, “perfection… doesn’t seem like a crazy idea” after all. They maintain that perfection in manufacturing is achieved when the four initial principles are allowed to “interact with each other in a virtuous cycle. In general;
Getting value to flow faster always exposes hidden muda (Japanese, waste) in the value stream. And the harder you pull, the more the impediments to flow are revealed so they can be removed. (Womack and Jones, 1996)
What is Six Sigma?
Oakland and Followell (1990:356) describe Six Sigma as a disciplined approach to improving performance. They emphasise its ability to improve process capability through “rigorous data gathering, analysis and action.” A Six Sigma programme, apart from delivering cost saving to an organisation, also retains and improve value for the customer. “While the old Six Sigma was just a metric, the new Six Sigma is a management system for running the business on a day-to-day basis.” In its most basic sense, Six Sigma stands for six standard deviations from the mean. Gygi et al (2005:16) define a Six Sigma performance as the statistical term for a process that produces less than 3.4 defects or errors per million opportunities. Motorola (which championed the approach to help improve competitiveness) argues that:
A process or procedure that can achieve plus or minus Six Sigma capability can be expected to have a defect rate of no more than a few parts per million, even allowing for some shift in the mean. In statistical terms, this approaches zero defects. (Oakland, 1990:356)
The Six Sigma approach links the voice of the customer (VOC) to the voice of the process (VOP) by specifying “the variability required of a process in terms of the specifications of the product so that product quality and reliability are maintained to meet customer requirements. According to Taghizadegan (2006:4), at three-sigma (the level at which most world-class organisations operate) the cost of quality is 25 to 40 percent of sales revenue. At Six Sigma, it reduces the cost of quality to less than 1 percent of total revenue.
The Six Sigma methodology integrates tools and concepts from the fields of engineering, statistics and business management into a rigorous framework that seeks to solve quality problems and optimise processes. Ramberg (2000) lists several tools including Statistical Process Control, Advanced Diagnostic Tools, Planned Experimentation, Design for Manufacture, et cetera that have been integrated into the Six Sigma regimen. Tricker and Sherring-Lucas (2005:151-2) liken Six Sigma to a collection of tools or a toolbox “which can be used as appropriate to the process”. This is typically so because the originators of the approach designed a system that brought together concepts and tools from the world of quality management, cost reduction and process improvement into a coordinated, workable framework across the Define-Measure-Analyse-Improve–Control (DMAIC) cycle. Anbari (2002) summed the contemporary Six Sigma approach in the equation:
SIX SIGMA = TQM + Stronger Customer Focus + Additional Data Analysis Tools + Financial Results + Project Management
The strategic emphasis for Lean Six Sigma
In the face of fierce global competition, companies cannot continue to do things the same old way. The customer is king, and the marketplace determines the price that customers would normally pay for goods and services. Even companies that seemingly have a hold on their markets due to niche products or services cannot wave that banner for too long because businesses always stand the risk of being swept away by the flood of competitive marketing. Effectively, when a business competes on price, its best approach to remain solvent is to reduce the cost of producing its goods and services.
The drive to defect prevention, quality improvement, cost reduction, process optimisation and variation reduction begins when companies realise that there is a cost attached to every mistake or potential mistake – a lost customer, the need to do it all over again, loss of production time, or a general waste in resources. In fact, waste and mistakes cost companies between twenty and thirty percent of their combined revenues. The future for every business’ worth – its salt – is to pursue and implement systems that make them competitive in their marketplace.
Conclusion
Over the next episodes, I will be sharing concepts such as:
- Deconstructing the Lean Paradigm
- The Six Sigma Methodology for Improvement
- The Six Sigma Methodologies for Design
- Lean Six Sigma in a Digital Transformation Era
- Not Just a Manufacturing Thing- Implementing Lean Six Sigma in the Service Industry
- Conceptual Roadmaps and Pitfalls to Avoid in Implementing LSS Company-wide
I invite you on a wonderful journey as we explore the underpinnings of Lean Six Sigma together. Welcome on board.